Home | Issues | Articles | Experimental
Aviation Glossary | Video Hints
for Homebuilders | Q&A | A Personal View | Polls
From the Archives
August
1983- Sport Aviation - TONY BINGELIS
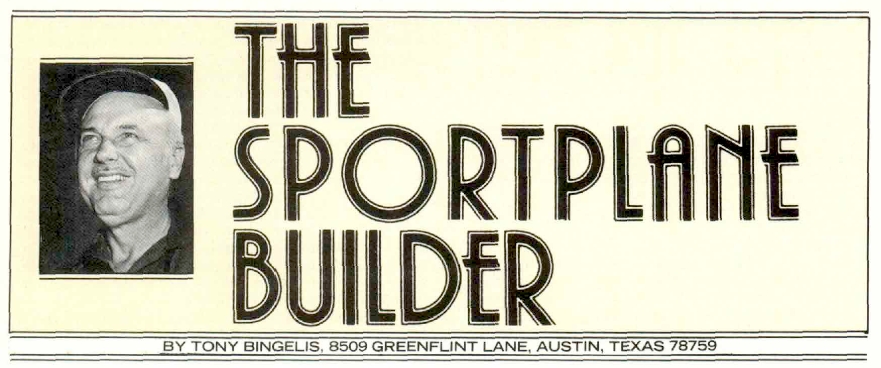
HOW TO BEND TUBING
SUCCESSFULLY
|
FORTUNATELY,
MOST OF our homebuilt projects do not require very much tube
bending. However, I assure you that these few components are
important and many of them are, for the most part, highly visible.
Being so visible, their fabrication merits your very best effort.
But giving it your best effort does not mean you have to make a big
production out of this tube bending thing. That goes for bending
steel tubes, copper tubes and aluminum tubes as well.
Anyone building a tube and fabric airplane will
probably encounter more opportunities for developing his tube bending
skills than he would if he were building a composite. These welded
tube aircraft are ordinarily endowed with nicely curved tail surfaces
made of small diameter steel tubing. Some of them also have tubular
wing tip bows, fuselage formers and seat frames as well. Builders of
other types of aircraft can add windshield and canopy bows, flap
handles and sometimes "S" shaped control columns to the
bent tube list.
Just about the only copper tubes used in homebuilts are the
oil pressure line and the primer lines. Even these are falling into
disuse as more builders switch to electrical gauges. These copper
tubes are a mere Vs" in diameter and may be easily bent by hand or
formed around an empty tin can or jar of the proper diameter. No
serious tube bending problem here.
Aluminum tubing is not only used for fuel lines,
it is also used for windshield and canopy bows and wing tip bows,
too. These being tubes of a larger diameter present bending problems
similar to those experienced with steel tubes. Ultralight builders
utilize a lot of pre-bent aluminum tubing in structural elements but
these components are, ordinarily, purchased pre-cut and pre-bent from
the factory or supplier. Aluminum tubes are important in fuel systems
and so are the bends you make in them. After all, why use a fitting
where a bend in the tubing will do as well? Tubing bends are much
lighter, cheaper and, unlike fittings, can't leak.
Do not be lulled into thinking that simply because
1/8" aluminum fuel lines are rather ductile you can easily form
them by hand. You can, of course, but hand formed ends often become
flattened and have a poor irregular appearance. Such wavy flattened
bends are the usual result of
|
attempting to bend thin wall tubing to
small radii without the aid of a tube bender. A flattened fuel line
can restrict the flow of fuel and could, ultimately, fail in service.
What Happens When A Tube Is Bent?-
|
To make a bend in the middle of a piece
of tubing, you would grasp it at each end, right? Then you would
place it over some hard curved surface and push down hard on both
ends of the tube . . . and the tube will begin to bend. If the radius
of the underlying object (form) over which you are making the bend is
large, the bend will be large and gentle and the tube will retain its
round cross section. If, on the other hand, the surface beneath has a
small radius, the curvature developing in the tube will be localized.
For the first few degrees of bend, the bend will develop nicely.
Then, you will notice that the tube is beginning to flatten. The top
side of the bend is now under increasing tension and has to stretch.
The tubing, however, is reluctant to do so and takes a short cut around
the bend causing that unwanted flattening in the tube. But, what
about the bottom side that is jammed against the "bending
form"? It is being severely compressed and although the tubing
resists this crowding it is beginning to show signs of buckling across
the tube diameter. If you continue the bending, the flattening on the
top side will become more pronounced while at the same time, the
crowded metal on the bottom side relieves the pressure by developing
more wrinkles. Ultimately, the tube will suddenly bend sharply and
fracture.
Thin wall tubing is more difficult to bend successfully
because it is very quick to flatten and buckle.
The larger the tube diameter, the greater the pressure
you must exert to make it bend. While you can easily form a 90° bend
in a Vs" diameter copper line that is only 6" long, you
simply cannot do the same with a similar length of %" tubing.
Not even if you had a form to bend it around. Why is that?
You Need Leverage
|
No matter how you go
about bending a length of tubing, you will find it much easier to do
if the piece is long enough. You can then take advantage of the
leverage it affords (you know the principle). A lack of sufficient
leverage could
|
48 AUGUST 1983
make it almost
impossible for you to form a bend near either end of a %"
diameter steel (or aluminum) tube. Always start with a long length of
tubing when bending it. The larger the diameter of the tubing, the
greater its excess length should be. Allow an extra 12" on each
end for tubing up to 3/4" in diameter. Allow even more for
larger diameters . . . you will need the added leverage it affords.
If you find you need more leverage, you can always slip in a steel
rod or slide a larger diameter tube over the end to serve as an
extended handle of sorts.
Equipment Needed
|
It should allow you to
make simple bends with a high degree of success provided it can
accommodate the diameter of the tubing you need to bend. Most of the
tubing we use in homebuilts is either 1/2" or 3/4" in
diameter (sometimes 5/8", too. If the tube bender you have
access to is made for larger diameter tubing you probably shouldn't
use it as it might cause your bends to flatten excessively. The
design of an electrician's tube bender is simple enough that you
could duplicate it for the size tubing you need to bend.
A simple plywood bending form nailed to a work
bench is a good basic bending device for large bends in small
diameter tubing. However, when cutting the form to shape you must make
its curve sharper as the tubing will have a tendency to spring back.
This sort of bending device is easy to use for uniform curves because
you can fasten one end of the tubing and pull the free end around the
form causing it to bend smoothly in one easy sweep.
An
improved variation of the plywood bending jig
(form) is one with its edges grooved to the diameter of the tube for
which it is intended. The groove is important. It reduces the
tendency for tubing to flatten and somewhat sharper curves or bends
in the tubing are possible. An even greater improvement would be to
make the routed groove somewhat deeper so that the tubing will nestle
in it beyond its half diameter. This added depth permits the walls of
the groove to exert a restraining effect against the tube's tendency
to flatten. It is equally important, when making any grooved pulley
or bending jig, for the grooved edges of the form to be strong enough
to resist the flattening and widening of the tube. A wood form,
particularly a plywood form, is rather weak in this respect so it
should have considerable edge distance between the groove and the
edge of the pulley, form, jig or whatever. A grooved aluminum
"pulley" would be much stronger but is harder to make if
you don't have a large hunk of aluminum plate or a metal working
lathe. Figure 5 shows some options for making grooved tube bending
devices, be they pulley types or the simple wood jig types. Figures 1
through 5 should give you enough ideas to help you devise a bending
device
of your own.
Click image for a larger view
|
You don't need much in
the way of equipment or materials to make good uniform bends. These
items are definitely needed.
1.
You will need a large rugged vise. The effectiveness of almost any
type bending device will be greatly improved by clamping it in a
heavy duty vise mounted securely on a solid bench. In addition to
freeing both hands (and in some cases, feet), it will enable you to
more precisely apply the bending pressure to the tubing. A substitute
for the vise would be a good solid immobilized bench to which you
could bolt a bending device horizontally.
2. Some sort of bending device is essential for
any bend exceeding, say 15° to 20° especially when that bend is
concentrated around a small radius.
3. A filler material (sand, bending alloy or salt)
for those hard to make bends.
4.
Templates cut from plywood. How else can you check the bend you are
making?
Tube Bending Devices
|
You can bend tubing
successfully with just about any simple homemade tube bending device
if it is properly made. You have a wide variety of types from which
to choose.
Locally
you might have access to some commercial tube bending machine. If so,
great . . . just remember to bring your templates, too.
Others of you might be able to locate someone who
has an Electrician's Conduit Bender and arrange for its use.
|
|
SPORT AVIATION 49
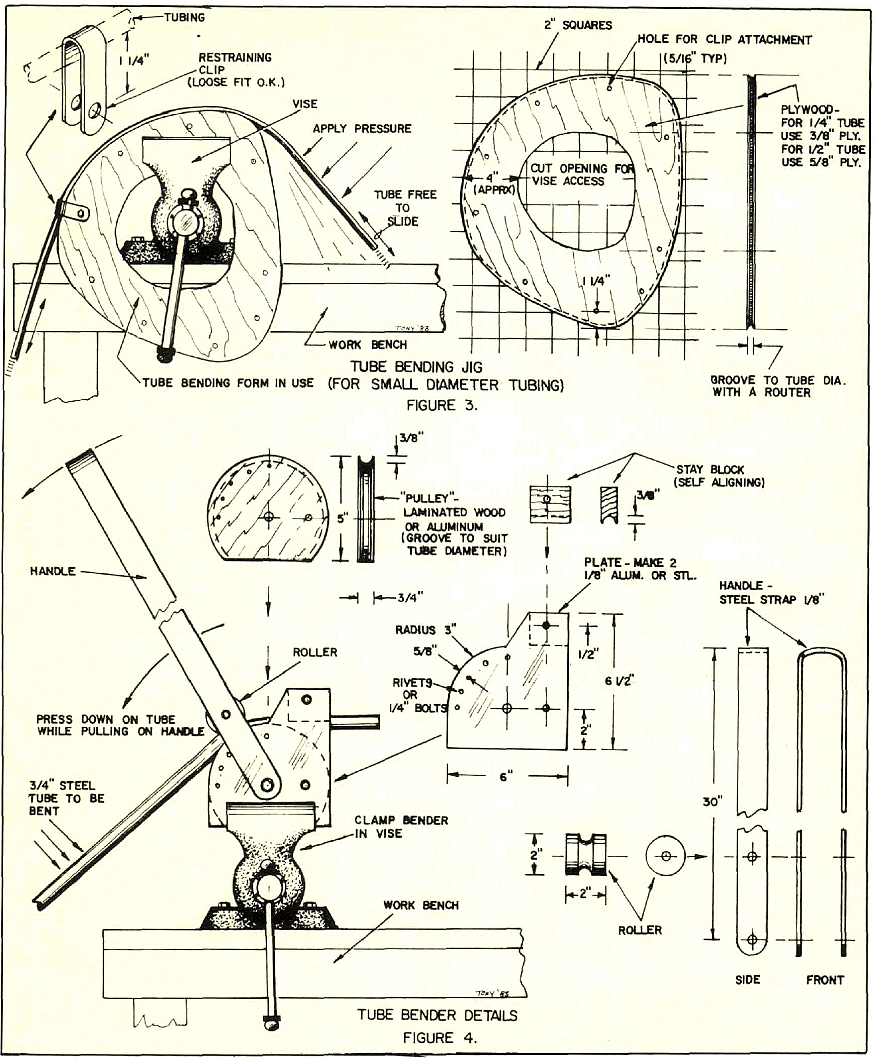
Click image for a larger view
|
Bending Procedures
|
|
Tubing in aircraft work is usually bent
cold. Contrary to what may seem logical and contrary to what you may
have heard, attempting to bend tubing by heating it can turn out to
be a lousy adventure. Most of us don't have the skill and patience to
play with a hot bend and will usually get unhandsome results. The problem
lies with localized uneven heating and poorly coordinated bending
pressures . . . to say nothing of impatience. Pressing a hot tube
against a bending form will surely cause it to flatten on the inside
of the bend. Hand bending it without the aid
|
of a form is likewise very difficult to
do successfully. In short, bend it cold.
Heating tubing to a red hot condition
does have a place in bending. Bending causes the metal to harden
somewhat. So, by heating the tubing you can anneal it and continue the
bending carefully after the tube cools. In other words, it is
possible to make bends over a smaller radius if you anneal the tube
once or twice as the bend progresses. This is a slow way but it can
make an otherwise severe bend possible. There is another way to
reduce the risk of making a poor bend. Use a filler material.
|
50 AUGUST 1983
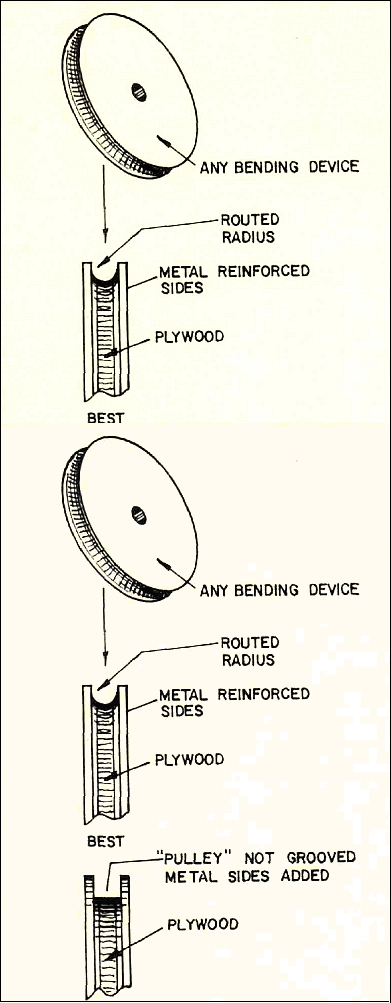
Click image for a larger view
The Use Of Filler Materials
It is easy to see that packing a tube
you want to bend with a solid material like sand or a molten bending
alloy will greatly inhibit the flattening tendency.
Before you attempt to bend any large diameter tube
(3/4" or larger), you should fill it with densely packed sand.
(I understand that salt works as well although I have never tried
it.) The sand has to be dry and well sifted to remove all foreign
matter and the larger grains of sand. Plug the bottom end of the tube
with a wood plug and pour in the sand. Tap the bottom end of the tube
repeatedly against
|
a solid surface (concrete floor). After
the tube is full of sand, the continued tapping will cause it to
settle and pack more densely. Add additional sand. After the sand
shows no further sign of settling, drive a wood plug into the top end
of the tube being sure it bottoms solidly against the sand. Your tube
is now ready for bending. The risk of a flattened bend will have been
considerably reduced. A more effective filler, of
course, is any of the commercial bending alloys, CERROBEND, for
example. These alloys have a very low melting point, some as low as
165° F. When this bending alloy is heated to its melting point it can
be poured into the tube you want b e n t . . . sure, plug the bottom
first. Cooling the tube in water will solidify the alloy and you are
ready for the bending effort. After completing the bend, the tube has
to be reheated to melt out the alloy. The material can be reused any
number of times. However, since it is unlikely that most of us could
find an economical source for a bending alloy, the sand treatment is
and will continue to be the one most used by homebuilders.
More About The Bending Process
You cannot hurry your
tube bending chore. It will ordinarily take much longer than you
would expect. Allow yourself plenty of time for bends that do not
have a uniform radius.
Most any bending device you use, with the
exception of a template-like bending jig, will have a rather small
diameter grooved pulley, roller or disc over which the tube will be
bent. Obviously, you cannot bend the tube very much in any one place
if your bend requires a radius many times larger than the bending
device pulley. That means the bending process may become quite long
as you have to bend a bit, check the bend in the tube against a
template, etc. As an aid to checking the accuracy of your bend as you
proceed, you should mark a center line around the tube to use as a
reference mark keyed to your template. (Use a black laundry marker on
aluminum tubes and a silver lead pencil on steel tubes.) Do not
forget to check the tubing after the bending is completed to be
sure that it is not twisted, as viewed from the ends. Lay
it on a flat surface for a quick check. If warpage is present, a
twisting pressure in the proper direction will take out the warp.
Recheck the tube's bend against the template again before
congratulating yourself on a job well done.
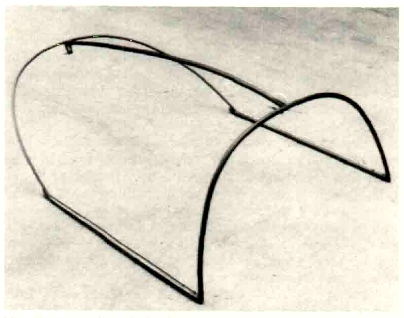
The component parts for this canopy frame were bent around a
4" homemade aluminum pulley. The tubing was not filled with
either sand or a bending alloy, however, the bends are probably the
minimum radius possible without such a provision.
|
SPORT AVIATION 51
|